The shift from silicon to silicon carbide in power modules promises lower power losses, increase power density and offer superior heat dissipation with advance packages. At KTH Royal Institute of Technology, Bhanu Singh, a PhD student, and supervisor Staffan Norrga, specializing in power electronics, evaluate lifetime aspects of the new type of module, in an SEC funded project.
Silicon versus Silicon Carbide
Traditional power modules for heavy electric trucks use silicon-based Insulated-Gate Bipolar Transistors (IGBTs). However, new modules are increasingly adopting silicon carbide-based Metal-Oxide-Semiconductor Field-Effect Transistors (MOSFETs). Singh believes that the silicon carbide alternative might initially present less reliability due to distinct mechanical properties but acknowledges that the advance packaging and materials could allow better exploitation of the full potential of silicon carbide.
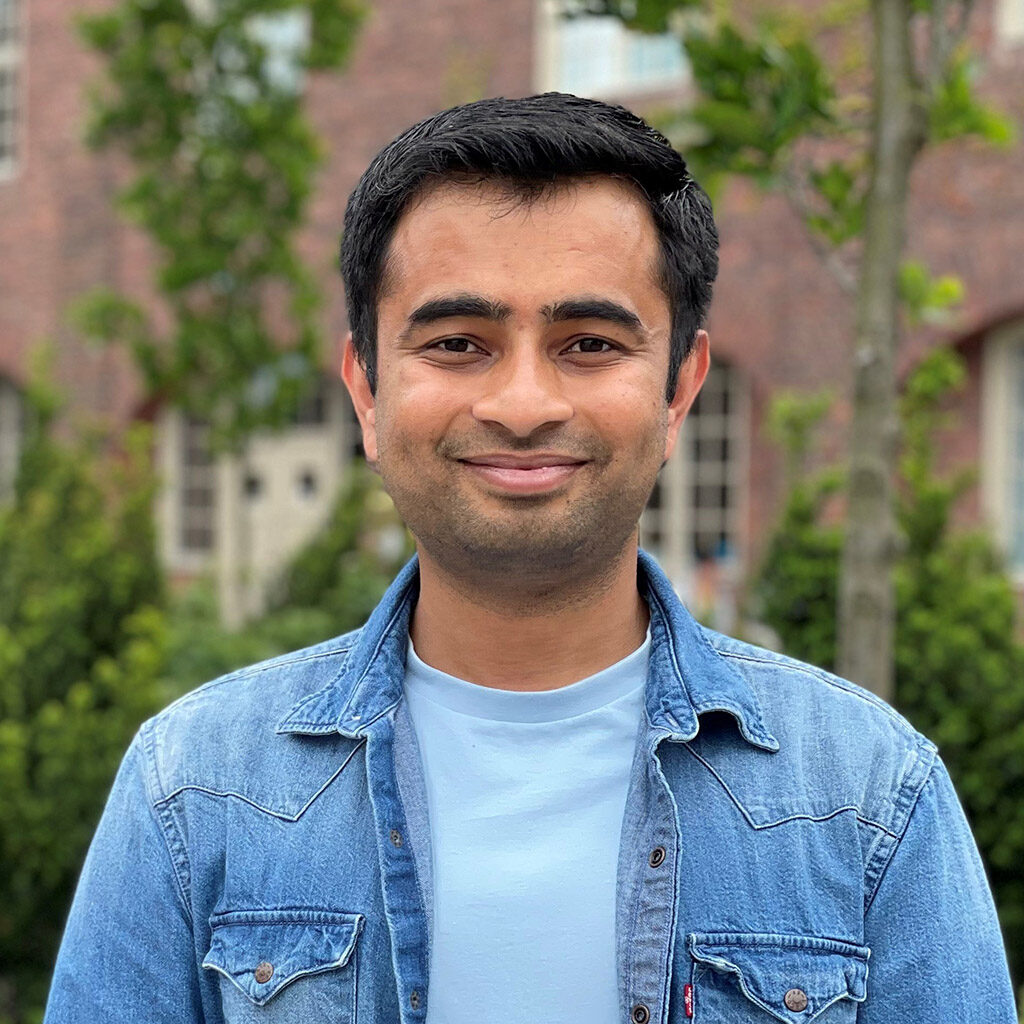
Advanced Power Modules and their Advantages:
More and more new advanced power modules that utilize new materials are being used. They promise better heat dissipation, which is essential as it enables modules to operate at higher losses. Higher heat dissipation means more generated heat is transferred to the environment, improving module performance. Moreover, these advanced packages can operate at higher power densities, an attractive feature for electric vehicle manufacturers who aim to use less silicon carbide in their packages.
“Advanced packages offer better heat dissipation, so the heat that is generated inside the power module will be transferred to the environment. They offer better thermal performance, you can operate the module at higher power density”, says Bhanu Singh.
The Road to Increased Power Density
In an ambitious roadmap, car manufacturers plan to increase power density up to 100 kilowatt per litre. This would result in higher losses, generating more heat inside the modules. Therefore, the need for advanced packaging is paramount to dissipate the resulting heat efficiently, ensuring the continued functionality and longevity of the power modules.
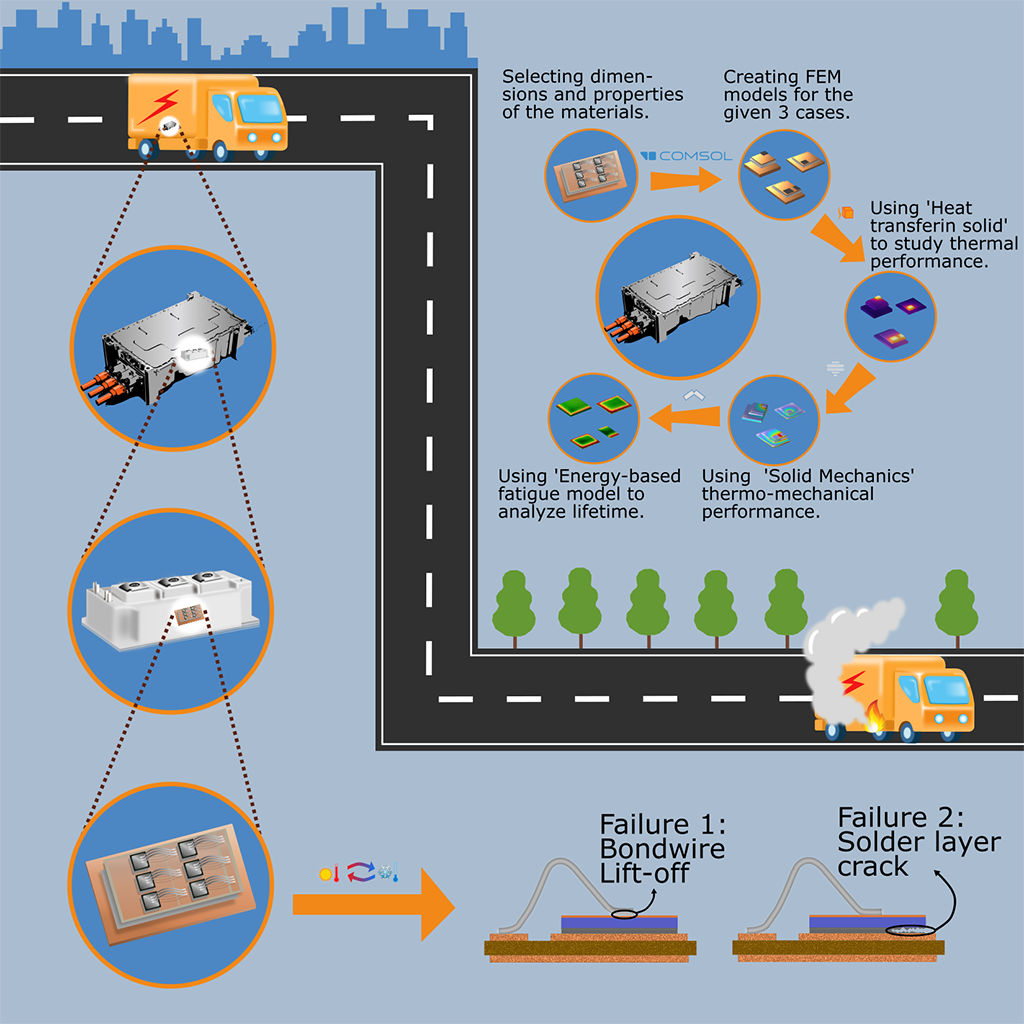
Challenges and Progress
Despite the progress, Singh’s project faces some hurdles. The validation of lifetime models and the fabrication of custom power modules have been delayed due to long lead times for semiconductor dies. Singh estimates that his project is 60-70% complete, with validation remaining the significant unfulfilled component.
Invaluable Connections
Working with the Swedish Electromobility Centre has given Singh opportunities to connect with industry professionals, learn from fellow researchers, and gain different perspectives.
“I feel very good working with the Swedish Electromobility Centre. I have been able to make a lot of contacts. I’ve attended all the SEC conferences like ‘Roads to the Future’ and ‘Emobility Days’ and met many people there. The best thing was the Autumn School which I attended in 2021. I met many professors and PhD students from different universities and learned a lot from their projects as well. Overall, it has been a really nice journey with the Swedish Electromobility Centre”, says Bhanu Singh.
Despite the challenges, Singh remains enthusiastic about his work’s potential impact, contributing to a greener and more efficient future.