Mobile work machinery, like wheel loaders and excavators, stands for about six percent of Sweden’s total carbon dioxide equivalents. A large part of the energy in these machines is passing through hydraulic pumps. There is a need to improve today’s electro-hydraulic pump units since they are unnecessarily large and inefficient.
The project Electric motor plus hydraulic pump fusion for electrification explores the most advantageous concepts to combine an electric motor with a hydraulic pump by addressing the criterions weight, volume, noise, and efficiency. Thomas Heeger is PhD student in the project.
First, who are you, Thomas?
I’m originally from Cologne, Germany. I have my master’s degrees from my home country where I also worked for some time as a development engineer at an automotive supplier, focusing on lubrication oil pumps. In late 2020 I joined this PhD project on electro-hydraulic pumps at Linköping University.
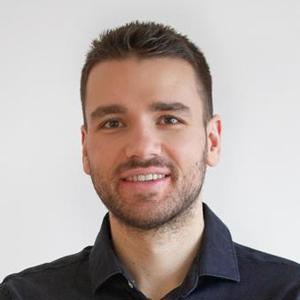
What motivated this project?
The motivation comes from the need to improve fuel consumption and reduce emissions. By decoupling the speed of the oil pump from the combustion engine, we can run the pump at the optimal speed for each operating point, minimizing energy input. This is crucial for meeting EU emission norms and reducing fuel costs.
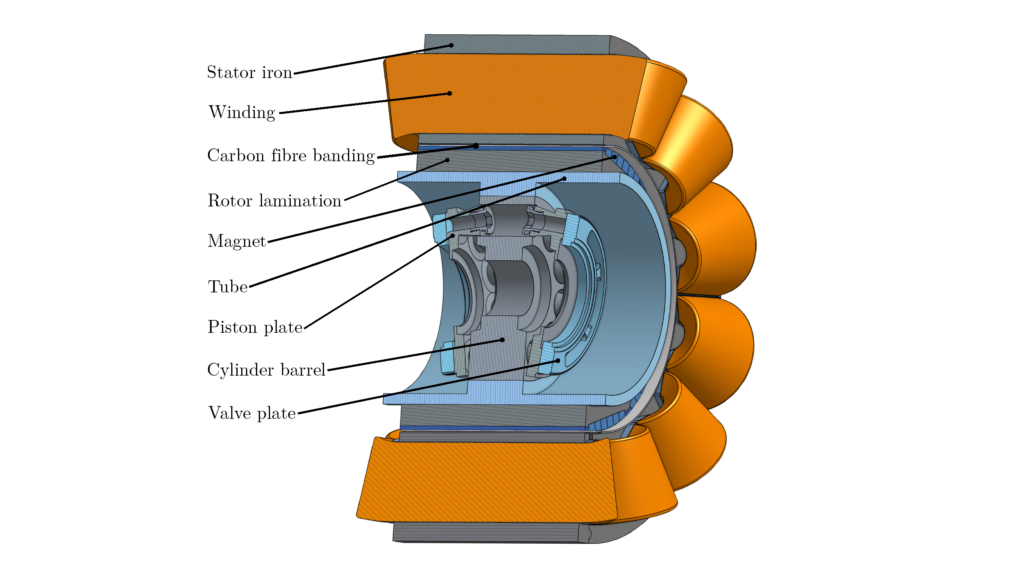
The aim is to combine a hydraulic pump with an electric motor into one compact module. This integration is intended to improve the compactness, efficiency, and noise behavior of the system. It is also an enabler for more advanced hydraulic systems, in which sharing losses which originate from supplying multiple actuators at different pressure levels from the same pump can be reduced. Hydraulics are very power-dense, and by placing the hydraulic pump within the volume of the electric motor, we can maximize compactness.
What are some of the challenges you face in this project?
I see three main challenges in this project.
First, traditional hydraulic pumps have been developed to match the capabilities of combustion engines. To fully exploit the potential of electric motors, the hydraulic pumps need improved efficiency, increase their speed range to support both lower and higher speeds, allow energy recuperation, and become less noisy.
Second, there are some obvious benefits when integrating the hydraulic pump in the core of the electric motor, for example increased compactness, the elimination of some components such as a coupling, a pair of bearings and shaft seals, as well as reduced external leakage and reduced churning losses at high speeds. However, this integration comes with many design choices, which require compromises. For example, one can either allow oil to enter the “air gap” of the electric motor, or install sealings to avoid this. An oil flow through the air gap can be used to add some cooling, but as oil has a higher viscosity than air, a larger air gap is needed to limit viscous losses. However, a larger air gap reduces the electro-magnetic performance of the machine. On the other hand, installing seals to protect the air gap from oil introduces additional components, and increases friction losses. We are currently updating our test rig to be able to test a prototype of an integrated machine.
The third main challenge is noise, which generally is a very complex topic. Counter-intuitively, removing the combustion engine which was the noisiest component can create new noise issues, as the noise from other components, especially the hydraulic pump, becomes more audible. Both the electric motor and the hydraulic pump create noise, and this depends on their individual designs, but also on their interaction. Knowledge on which effects contribute to noise at which frequencies for each machine is expected to be helpful to evaluate the first prototype.
How do you see the future of this technology?
I believe that integrating hydraulic pumps with electric motors will become more common as we continue to improve the technology. This approach not only enhances efficiency and compactness but also aligns with the industry’s move towards electrification. Companies like Volvo are already showing interest in these developments, which is very promising.
More information:
I plan to defend my PhD at the end of this year. That would be a nice Christmas present. For those who want to know more until then I would recommend my licentiate, or a recently published paper where we show the integrated machine. You are also welcome to contact me.
Licentiate: Design of Electro-Hydraulic Energy Converters : With Focus on Integrated Designs and Valve Plate Rotation
Paper: Methodology for Dimensioning of Integrated Electro-Hydraulic Machines
Contact: Thomas Heeger – Linköping University